Quels sont les avantages de l’azote ?
L’utilisation de l’azote (gaz inerte) dans le processus de brasage à la vague ou brasage par refusion présente de nombreux avantages.
Lecture : 4 min
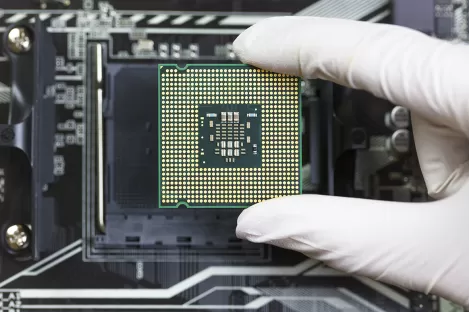
Avantages de l’azote pour le brasage à la vague
L’utilisation de gaz inerte (l’azote) dans le procédé d'assemblage des composants traversants, dans une machine de brasage à la vague permet, grâce à la diminution de la teneur en oxygène :
- de ralentir les phénomènes d’oxydation de l’alliage,
- d’augmenter sa fluidité,
- et aussi de réaliser de meilleures remontées dans les trous métallisés des cartes électroniques.
Les utilisateurs du procédé de brasage à la vague sous azote bénéficient de ces propriétés et des retombées économiques qui en découlent :
- La réduction de la formation de scories de l’alliage sans plomb à haute température.
- La diminution de la quantité de flux déposée sur les circuits.
- La maintenance réduite.
- La réduction des défauts de brasures et amélioration de la qualité du brasage.
Pour toutes ces raisons, le fonctionnement sous azote est reconnu par les fabricants d’équipements de brasage, qui proposent tous cette option de base sur leurs machines.
Avantages de l’azote dans le brasage par refusion
L’utilisation de gaz inerte (l’azote) dans le procédé d'assemblage des composants CMS dans un four de refusion, permet grâce à la réduction de la teneur en oxygène :
- de ralentir le phénomène d’oxydation des brasures,
- de permettre l’utilisation de crèmes à braser moins actives par rapport à celles utilisées sous air,
- d'obtenir des cartes plus propres avec moins résidus sur la surface de la carte,
- d’obtenir des joints de brasure plus fiables et plus robustes avec une bonne résistance mécanique.
Pour toutes ces raisons, la production des cartes électroniques sous atmosphère inerte est reconnue par la profession comme une solution pour optimiser le niveau de qualité de brasage des composants, permettant une diminution des défauts de joints brasés, observable dès l'étape de contrôle après brasage.
Avez-vous des questions sur nos solutions pour l'assemblage de circuits intégrés ?
Utilisation de l’azote et la sécurité
En matière de sécurité, les systèmes de mesure de la teneur en oxygène du poste de travail participent à l'action de prévention indispensable pour éviter des incidents, lors de l’utilisation des gaz inertes comme l’azote.
En effet, les gaz inertes injectés dans un équipement peuvent causer un déficit en oxygène, avec un risque d’asphyxie (Anoxie), s’ils ne sont pas évacués vers l'extérieur par les extractions.
En dessous de 18% d’oxygène dans l’air, les premiers symptômes peuvent se faire ressentir. De façon à vous prémunir de tous risques industriels, nous vous engageons à vous référer à votre code du travail ou alors à questionner les équipes Air Liquide qui pourront travailler avec vous la gestion des risques sécurité.
Savez vous la différence entre le brasage et le soudage ?
Brasage et le soudage sont souvent confondus dans le langage commun de l’écosystème de l’assemblage électronique.
Une soudure s'obtient par élévation thermique au dessus du point de fusion de deux matériaux identiques : l'un étant le métal de base, l'autre le métal d’apport. Les températures élevées sont celles qui correspondent à la température de fusion des deux métaux. En métallurgie, différents types de mélanges de gaz assurent la protection des pièces métalliques soudées.
Par contre, le processus de brasage est une opération d'assemblage qui s'obtient par fusion d'un alliage d'apport (par exemple un alliage à base d’étain et d’argent ) sans fusion du métal de base. Le point de fusion du métal d’apport doit donc être à une température inférieure à celle du métal de base.
Avez-vous des questions sur nos solutions pour l'assemblage de circuits intégrés ?
Nos solutions
Avez-vous des questions sur nos solutions pour l'assemblage de circuits intégrés ? Remplissez le formulaire de contact!
Nos experts prendront contact avec vous dans les 48 heures!Vous voulez en savoir plus?
En savoir plus
- Procédés gaz pour l’assemblage électronique
- Assemblage des composants électroniques sur circuit imprimé par brasage à la vague sous azote
- Brasage par refusion sous azote
- Technologies de test pour la fiabilité électronique (HALT & HASS)
- Eco Chiller
- Stockage des composants électroniques sous atmosphère d’azote
- Audit et Expertise pour l’assemblage électronique
- Stockage de composants en Dry P Cabinet
FAQ
- Quel est le rôle de l’azote dans le brasage ?
- Pourquoi stocker les composants et cartes électroniques dans une armoire sèche à l’azote ?
- Comment sont conçues les cartes electroniques ?
- Quelles sont vos normes d'assemblage de circuits imprimés ?
- Comment monter un composant sur pcb ?
- Qu'est-ce que le processus d'assemblage de pcb?
- Quel est l'avantage de l’azote dans le brasage à la vague et le brasage par refusion ?
- Quel est l’avantage d’utiliser un échangeur thermique dans mon usine pour refroidir mon eau de process ?
- Quel est le coût de l’azote livré sous forme liquide et produit sur place ?
- Quels sont les dangers de l’azote ?
- Est-ce que la fourniture en azote est fiable ?