Le rôle de l’argon dans le cladding des disques face à la norme euro 7
L' application de l’argon pour le revêtement des disques au laser crée une atmosphère inerte qui protège de l'oxydation. L'argon de haute pureté garantit un rechargement (cladding) des disques de frein de haute qualité, fiable et sans défaut.
Lecture : 4 minutes
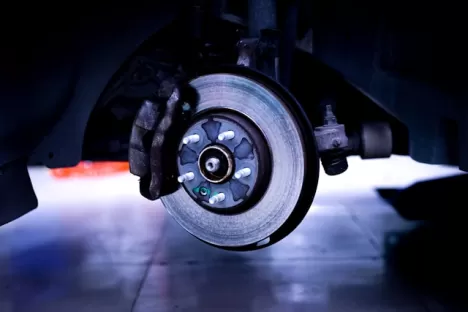
Alors que l’industrie automobile continue d'innover pour une plus grande efficacité et durabilité, le rôle de l'argon dans les processus de fabrication avancés, tels que le revêtement de disques au laser, est un facteur clé pour atteindre ces objectifs.
L'argon joue un rôle indispensable dans le processus de revêtement des disques laser car il fournit une atmosphère protectrice, en garantissant l'intégrité et la qualité du matériau de revêtement. Son utilisation est cruciale pour la production intensive de composants de haute performance qui répondent aux exigences rigoureuses des constructeurs automobiles.
Besoin d’information sur le rôle de l’argon dans le cladding des disques ?
Qu’est-ce que le laser disc cladding ?
Le rechargement de disque par laser est une technologie de fabrication qui consiste à déposer de la matière sur une pièce. Un faisceau laser de haute puissance fait fondre de la poudre métallique qui est projetée sur le substrat. Ce procédé est largement utilisé dans diverses industries, notamment l'automobile, l'aérospatiale et la fabrication métallique, dans le but d'améliorer les propriétés de surface du métal telles que la résistance à l'usure et la corrosion ainsi que la résistance mécanique. L'un des éléments essentiels de ce processus de fabrication est le gaz de protection, l'argon étant un choix courant en raison de ses propriétés uniques.
Quel est le rôle de l’argon dans le revêtement ?
L'argon, un gaz inerte, joue donc un rôle essentiel dans le processus de revêtement des disques de frein. Sa fonction première est de fournir une atmosphère protectrice autour de la poudre fondue par le laser. Cette protection est cruciale car elle empêche le métal liquide de réagir avec les gaz présents dans l’atmosphère tels que l'oxygène et l'azote. Ces réactions peuvent compromettre l'intégrité de la pièce produite et entraîner des défauts, comme une mauvaise adhérence, ainsi que des propriétés mécaniques inférieures.
En utilisant l'argon comme gaz de protection, les fabricants s'assurent que les matériaux de revêtement restent optimisés et exempts de réactions chimiques indésirables, ce qui permet d'obtenir des produits finis de meilleure qualité et plus fiables et de réduire l'émission de particules métalliques à provenance des freins.
Avantages de l’utilisation de l’argon dans le laser cladding
Les normes orientent l'industrie automobile vers des véhicules plus propres et plus économes en carburant, réduisant ainsi la pollution de l'air dans les villes. Elles amènent également les constructeurs à adopter de nouvelles technologies pour améliorer la conception des véhicules afin de répondre à des exigences plus strictes en matière d'émissions (les émissions de CO2 ainsi que la réduction des poussières fines constituent un objectif important).
La solution de revêtement laser est une réponse à la réglementation européenne EURO 7, qui vise à minimiser l'impact environnemental des émissions des disques de frein.
Besoin d’information sur le rôle de l’argon dans le cladding des disques ? Veuillez remplir notre formulaire de contact.
Nos experts vous répondront dans les plus brefs délais.En savoir plus
- Industrie automobile
- Solutions vecteurs de la transition énergétique du secteur automobile
- Solutions pour le revêtement laser des disques de frein
- Les solutions gaz pour les batteries au lithium
- Hydrogène pour les véhicules électriques à piles à combustible
- Gaz pour la fabrication et les tests des réservoirs d'hydrogène dans les véhicules
- Alimentation en hydrogène des moteurs à combustion interne des véhicules