Oxycombustion pour le recyclage de l'aluminium
Pour recycler des produits en aluminium, les fonderies s'efforcent depuis longtemps d'améliorer l’efficacité énergétique des fours de refusion. L’explosion des prix de la ferraille après tri incite les fonderies à recourir à des qualités moins chères qui contiennent des matières organiques.
Lecture : 4 min
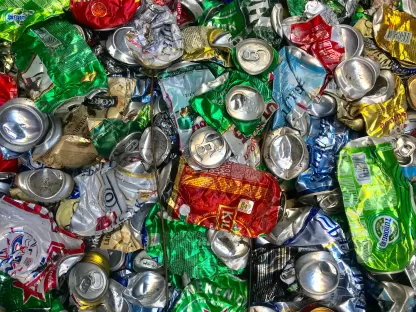
Les défis des fonderies
Pour répondre à cette tendance, Air Liquide a développé une technologie d’oxycombustion qui contrôle la température des fumées dans les fours et réduit la consommation de combustible. Les matières organiques présentes dans les déchets d’aluminium ne brûlent pas dans la cheminée, mais dans le four pour fournir de l’énergie au processus de fusion. Cette technologie s’appuie sur l’utilisation d’un brûleur oxy combustible breveté qui optimise les différentes phases de transfert thermique avant de couler l’aluminium en lingots.
Au cours des dernières années, Air Liquide a équipé un grand nombre de fours de refusion d’aluminium avec cette nouvelle technologie qui donne de bons résultats en termes d'économies de combustible.
L’oxycombustion
La plupart des fours de fabrication d’aluminium en Europe ont été convertis à l'oxycombustion pour améliorer leur productivité (réduction du “tap-to-tap”) et diminuer leur coût énergétique en réduisant la consommation de combustible.
L'oxycombustion améliore le transfert thermique vers les matériaux à fondre et produit moins de fumées ; le système de traitement des fumées pour respecter les normes de rejets est plus compact et moins coûteux.
Air Liquide a développé un nouveau concept de brûleur oxy combustible pour tirer pleinement parti des avantages de l'oxycombustion en termes de réduction du besoin en combustible et du temps de fusion, avec un rendement métallique élevé.
Besoin de conseils sur la mise en oeuvre de l'oxycombustion ?
La technologie Air Liquide
La conception du brûleur d’Air Liquide offre deux modes de combustion possibles.
Le mode dynamique utilise une flamme dirigée vers les matières premières pour en accélérer la fusion, puis une flamme horizontale pour éviter l'oxydation de l'aluminium liquide.
Le mode étagé utilise une combustion sans flamme pour réduire les émissions d’oxyde d’azote (NOx).
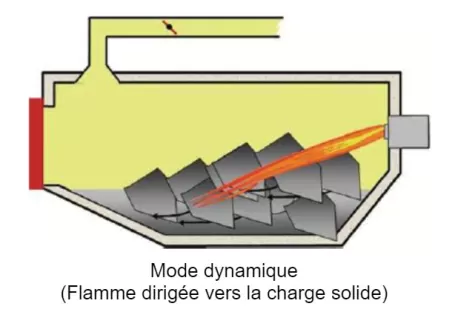
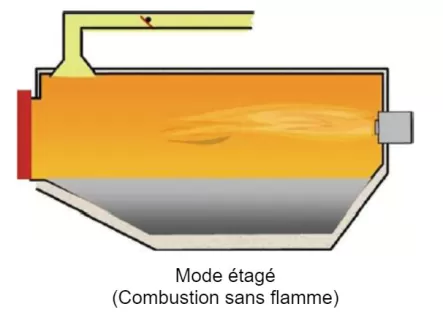
Cas pratique
Exemple de deux fours rotatifs identiques de 12 tonnes dans une fonderie qui fait du traitement de ferraille d’aluminium pour produire de nouvelles pièces moulées.
Le premier four est équipé d'un brûleur oxy combustible standard de type "pipe-in-pipe" ; le deuxième four est équipé d'un brûleur oxy combustible d’Air Liquide. Le deuxième four a un temps de fusion plus court. Il faut attendre la fin du cycle du premier four avant de pouvoir couler le contenu des deux fours en même temps.
Pour éviter une consommation excessive de gaz et des pertes d'aluminium, le deuxième four est démarré une heure après le premier. Le mode de combustion dynamique est privilégié pour accélérer la fusion pendant la première moitié du cycle de traitement, tandis que le mode étagé est utilisé quand l'aluminium a commencé à fondre.
Sur plusieurs mois de fonctionnement, le brûleur d’Air Liquide a une consommation de gaz naturel de l'ordre de 35 Nm3/tonne, inférieure de 3 Nm3/tonne à celle du brûleur standard de type "pipe-in-pipe". La durée d’un cycle (“tap-to-tap”) est de 9 heures pour le premier four et de 8 heures pour le deuxième. Le rendement métallique est conforme aux spécifications.